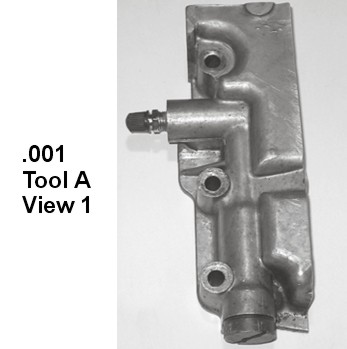
|
Tool A
View 1
a.
|
Cut approx 6" x 2
½" corner from an extra 3rd piece. |
b.
|
Tap hole indicated
1/8 NPT and screw Schrader valve in place. |
c.
|
Install piston,
dowel rod, copper seal ring and plug in relief valve bore. |
|
|
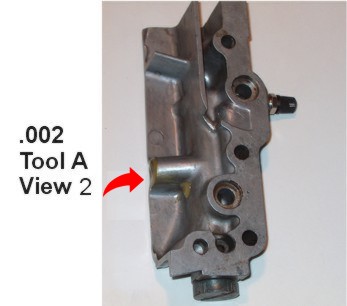
|
Tool A
View 2
a.
|
Plug
hole solid with rod
& epoxy. |
|
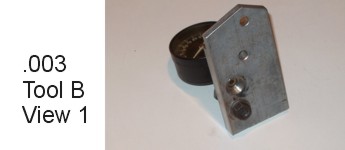
|
Tool B
View 1
a. |
Fabricate
block
for mounting on oil cooler pad. Note that
step is req’d so that one end will fit over M6 stud in top of case and
other end will be thick enough to provide for counterbored hole for oil
cooler seal and threaded hole for pressure gauge. Read ahead [I
happened to have a piece of aluminum that had 2 corners cut and a hole
in it.] |
b.
|
Counterbore
hole for oil cooler seal.
|
c.
|
In center of
counterbore, tap drill and tap 1/8" NPT to receive pressure guage.
|
d.
|
Drill 11/32" for use
in bolting tool to case using hole for oil cooler stud. M8 bolt &
nut can be seen in pic.
|
|
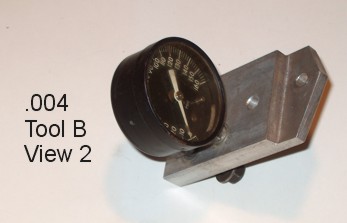
|
Tool B
View 2
a. |
Drill 1/4" hole
at point [point not necessary] for fitting over M6 stud in top of case.
|
|
Procedure:
- Place Tool A over studs on left case half and fasten
w/ washers and nuts.
- Place Tool B and cooler seal on cooler pad. Fasten to
M6 stud and use M8 bolt, nut and washer to fasten to case ala cooler
stud..
- Pressurize system to approx 120 psi. Brush soapy
water around oil
cooler pad to look for
leaks and/or listen for air escaping, if system is isolated -- watch
for loss of pressure on guage (assuming test system has no leaks.)
|
Note: These tools and procedure
will only test for leaks on the inlet side of the oil cooler.
In >40 years of fiddling with 356s, I have never seen a case leak at
the discharge side of the cooler.
|