|
Weaving Shuttle
A weaving shuttle is essentially a boat which ferries a bobbin of thread across the river of a loom's warp threads in an orderly and expedient fashion. When a cloth is prepared to have the next in a series of threads woven into the fabric, the thread must pass from either left to right and back or one end of the work to the other across warp threads. Over the centuries, a number of ways have been devised to transport this thread. While one could toss a ball of thread, or a bobbin on which it is wound, from one side to the other, weavers have devised containers for bobbins which offers several advantages. Shuttles by their shape and weight provide for speedy transport of the thread.
We should say that there are still some projects which the weaver may wish to use a cut length of thread. This practice eliminates transferring the thread from its spool onto the user's bobbin. This can be seen in tapestry weaving such as Southwestern Indian rugs. If the weaver is unsure of the length of thread required, they may not wish to cut a segment of thread which could be of insufficient length resulting in a possibly visible dreaded knot.
This page is presented to show several of the types of shuttles we have collected. We have others, but this page will try to shed some light on basic shuttle construction--at least the way Gramps would have done it.
|
First, we present different types. The type pictured above is a "Boat Shuttle" for obvious reasons. One could put your bobbin of thread in the larger wooden boat, install a cloth sail and you could sail it across your pond. The small shuttle has a hole in the bottom, which may be a problem for this explanation but hopefully you get the idea.
Below are two different examples of boat shuttles. The top shuttle which is lenticular shaped is probably of Eastern European origin. The lower sinusoidal shape is American and Western European. They serve the same purpose. Other than the footprint, significant differences can be seen in the bobbin size particularly in its length and thread storage capacity. Thread which exits the shuttle normally in the center would draw more evenly from the lower example. The top model is slightly shallower which would require a shorter shed of warp threads.
Weavers can debate over which style they prefer, but Elizabeth prefers the lower shape because of its "feel." The traditional style evolved over the years and fits the natural contours of a weaver's hand.
The shuttle is tossed with the weaver's index finger on the shuttle's tip. When caught by the other hand the shuttle should land in such a way that it is ready to be tossed back in the opposite direction of travel.
Shuttles are made from a variety of hardwoods including fruitwoods, dogwood, and maple. The hardwoods make it possible to give the shuttles a slick finish.
|
Shuttles Compared
The top shuttle is an open-bottom boat design while the lower classic model has a closed bottom boat design even though there may be a hole in it.
The open bottom boat design has a feature that permits the weaver to place their fingers on the bobbin. This may be advantageous because when the shuttle is caught, the bobbin must be held in place while an arc is formed across the warp prior to beating-in the thread.
|
Eastern European Shuttles
There are two parts that make up a boat shuttle. The boat is the carrier and the second part is the axle.
Some bobbin supports or axles are made of metal which tend to be straighter than twigs. Both types are shown above.
Bobbins are bobbins and not shuttles. Bobbins fit in shuttles and as the navy would say, "A boat fits on a ship." Of course, a boat shuttle is of little use without a bobbin. The converse is not true.
Bobbins hold the woof or filling thread and could be wool, cotton, etc.
Today's bobbins are factory-made with most being made of plastic or styrene. However, for centuries bobbins have been made of wood in one shape or another. It their simplest form, home-made bobbins were fabricated by cutting a length of elderberry stalk then pushing the pith from its inside. The image below shows a home-made bobbin made this way. Bobbins or quills can also be slips of paper, or cornhusks or another material that could be wrapped around the bobbin winder's spindle.
|
A study of anatomy of American boat shuttles reveals how they were made. The picture below shows how Gramps used a brace and bit to bore a hole into the shuttle to within 1/8-inch from the bottom. The score marks on the side were made by the bit. Shuttles in our collection fabricated this way reveal the openings were drilled with 1-1/4 and 1-1/2-inch bits. Three holes were drilled and the wood removed to form the elongation.
Shaping a Shuttle
All parts of the shuttles were finished to varying degrees perhaps either due to the skill of the wood carver or the tools he had available. Remember that many of these folks did not have sandpaper and would often use a broken piece of glass or a sandstone rock to smooth the surface.
A small screw on the bottom of the bit which pulls it thru the wood broke through the bottom which explains why some shuttles have three holes on their bottom. In most examples we have, the area between the three holes is simply removed because the wood splinters and gets hung up on the warp threads. Examples of how the screw holes are treated can be seen on the four shuttles below.
|
The image above shows how four different carvers treated their shuttle's bottoms after drilling three holes to create a cavity. The left shuttle shows that the pilot screw barely penetrated the bottom. The remaining shuttles show how pilot holes were dealt with.
|
In a minority of cases, the round opening was squared-off which would greatly increase thread storage capacity.
|
The bottoms of these shuttles shows various treatment of the underside or the side that slides across the warp threads. This is done in an effort to reduce friction or drag. From an engineering standpoint, longitudinal grooves also produce directional stability like sled runners. The bottom of the left shuttle is unadorned. The next shuttle, which was carved entirely by hand has a concave depression carved from one end to the other. The third shuttle was formed by a brace and bit as explained above and the maker cleared the wood between the three pilot holes and also added rails on either side. The right-hand shuttle shows a raised area around the shuttle perimeter. Wood between the three pilot holes was not removed
Note also that considerable effort was expended to polish to underside of most shuttles to allow them to glide across the warp threads.
Based on the above discussion, it would appear to this writer that the left-most shuttle would have the maximum drag and least stability while the right-hand shuttle would probably want to follow an arc. The two center shuttles are preferable models. Some engineering or textile arts student could do a thesis on the effects of all this rambling!
|
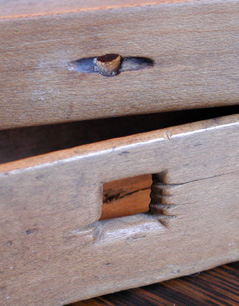 |
Thread, as it passes through eyelets, can cause wear to the opening. Flax is particularly noted for wearing away wood it passes over.
The grooves in the lower eyelet were cut by the passing of thread, probably flax.
|
|
Wear Guards
Shuttle eyelets show different treatments. Some eyelets are simply holes carved generally in the center. We have several examples where the opening is carved on the end of the spool. However it seems this configuration would pose problems in maintaining consistency as the shuttle is tossed from side to side.
There are several examples we have seen to reduce this effect. The image above left shows how small brads were driven just inside the eyelet and its surface now shows no sign of wear. Note wear on the unprotected eyelet hole on the right-hand image.
Some shuttles made today offer an elongated eyelet for better thread extraction from the bobbin.
|
There are several ways to secure the axle to the bobbin. Some twigs are simply forced into a slit slightly smaller than the axle. For more repeated use and better security a tiny dowel keeper is slid above the axle securing it in place. This bobbin has a metal axle which is reasonably inflexible and well suited for this method of securing it. The axle's opposite end is inserted into a retaining hole.
The shuttle above shows a cutout for clearance when using a bobbin with a disc on its end.
|
Double-Boat Shuttle
Double-boat shuttles carry two bobbins. Two threads of the same or different colors or sizes can be woven simultaneously. This beautiful piece is made from tiger maple and has elongated eyelets.
|
Ski Shuttle
Ski Shuttles derive their name from the shape of its runner. Ski shuttles are used for heavy yarns and rags. They are commonly used in manufacture of rag rugs. Long shuttles--about 24-inches--store longer lengths of weft material. They toss easily through the warp threads and the hook opening prevents snagging upper warp threads while in route.
|
Rag Shuttles
Rag shuttles are shown above and below. Rag shuttles are wound with heavy yarn or strips of rags. They are most often used in manufacture of floor rugs. The shuttle above reveals that its former owner had trouble keeping the ends together. This person probably did not have access to good glue like we have today so they secured the ends together with flax yarn. A problem this patch created was that now the yarn or rags had to be wound around the patch strings. It is a nice shuttle with good proportions.
The rag shuttle below was made of walnut for Elizabeth by Jim. He used his lathe and turned a shoulder on dowels that formed a mortise and tenon joint for a stable connection. The ends were shaped on a band saw then sanded and finished.
|
Homemade Rag Shuttle
|
End Delivery Shuttle
End-delivery shuttles or end-feed shuttles are typically used for mechanized looms. However, shuttles like the one above are hand thrown. (Machine thrown shuttles typically have metal tips.) These shuttles have the advantage of built-in thread tension adjustments. Some end-feed shuttles require that thread be fed through small holes. Newer shuttles are faster to prepare for weaving.
|
Netting Needle
Netting needles were created to make or mend fish nets. However, weavers have found that they make nice little shuttles for weaving on small looms.
|